神奇的深海“吸盘”——深海井口吸力锚技术
责任编辑: 陈慧
基金资助: |
|
作者简介 About authors
宋刚,博士,正高级工程师,主要从事海洋地质钻探、海域天然气水合物钻采工艺器具装备等方面研究。
本文引用格式
文图/宋刚.
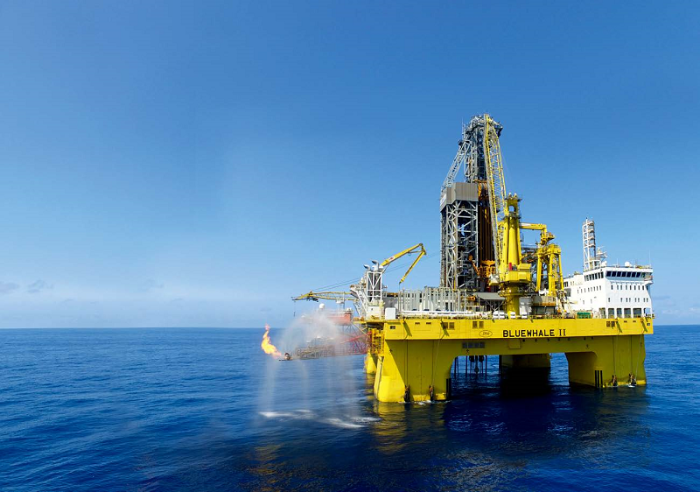
占地球总面积70%的海洋为人类提供了取之不尽,用之不竭的资源,广袤的海洋给人类带来海阔凭鱼跃般的遐思,深邃的海底世界更是蕴藏着人类赖以生存的油气资源,人们对深海探索从未停歇。随着海洋油气资源的开发走向深海,海洋工程领域相继出现各种系泊在海上的浮动式结构物,将这些庞然大物牢牢地固定在海底的技术尤显重要。
其来有自——深海“吸盘”的由来
随着海上油气钻采开发如火如荼地开展,对钻采井口的安全稳定性要求也随之增高,为确保井口防喷器在松软无比的深海淤泥之上稳如泰山般矗立,科学家发明了深海井口吸力锚技术。在我国第二轮海域天然气水合物成功试采中,深海井口吸力锚将重达400余吨,高10余米的井口防喷器稳稳地吸附于海底,状若深海“吸盘”,其作用不容小觑。
吸力锚原理,在20世纪60年代提出,20世纪70年代后期进行了原理性试验,1980年在欧洲北海丹麦油田的系泊储油装置上首次应用。我国于1986年由天津大学与中国人民解放军海军在浙江舟山进行了浅海(水深17米)、小尺寸吸力锚(直径1.5米,高3.5米)原理性试验,并于1994年首次在曹妃甸成功安装了两个系泊吸力锚(直径3.2米,高6米)。
深海吸力锚为一顶端封闭、下端敞开的钢筒,顶端留有抽吸孔。海上作业时,将吸力锚悬吊至海底,吸力锚在自重作用下慢慢沉入淤泥层一定深度。接着,通过布置在吸力锚顶部的吸力泵将钢筒内的海水从抽吸孔向外泵出,使钢筒内外形成压差,从而将吸力锚向下压入至更深的淤泥层,直至吸力锚顶盖下部与泥面接触,最后吸力锚就深深地嵌入到了泥层里。从外部看,犹如一个大型钢制“吸盘”牢牢吸附在泥面上。我国对吸力锚的研究和应用主要集中在系泊方面,利用吸盘与泥面强大的吸力,为海面上移动的船只或其他漂浮物提供固定位置的拉力。井口吸力锚是在顶部封盖的钢筒中间,从顶部向下垂直同心布置一个较小直径钢筒,最终形成一个顶部封闭、中间有一贯穿钢筒,具有环状空间的钢型结构,井口吸力锚中间贯穿式的钢筒是钻采油气的通道。
我国海域天然气试采技术处于世界领先水平,与之配套的深海井口吸力锚装备,使我国成为继挪威和荷兰之后,世界上第三个对深海井口吸力锚技术装备拥有完全自主知识产权的国家。
抽丝剥茧——解密深海“吸盘”
深海井口吸力锚作业环境在1 000多米水下,从设计到建造,直至最后的沉贯安装会遇到哪些难题?科研人员是如何解决的?深海“吸盘”还有哪些奥秘?
所承之重尤难计——承载力计算难度大
吸力锚承载能力的计算是研制吸力锚首要解决的问题。首先,要确定目的地层是否适合安装井口吸力锚,不同的海底淤泥质地层具有不同的黏性、硬度和砂土含量,承载和吸附能力也不尽相同;其次,要根据需求设计井口吸力锚结构尺寸和结构大小,即需要明确多大尺寸的吸力锚才能承载包括“井口防喷器”重量在内的隔水管、海水洋流的动载荷。井口吸力锚由于其特殊的双层筒状结构,目前国内外海底结构物设计规范中尚无成熟的可供参考的计算公式和依据。

吸力锚越大承载能力越强,但质量相应也越重,所需的建造、运输和安装成本相对越高。因此,最为经济的做法就是设计满足需求的最小结构尺寸的吸力锚。设计要求具备一套理论和算法,需要科研人员将所有的边界条件依次清晰罗列,数据包括获取的地层参数、动静载荷要求,等等,将地层剪切力和钢土摩擦系数通过室内实验初步掌握,并采用理论计算和有限元模拟软件两种技术手段进行计算,给定承载条件,设定安全系数,初步算出结构雏形,确定吸力锚的直径和高度。为了验证计算的准确性,找出理论计算数据的偏差,科研团队设计建造了一小型井口吸力锚原型机,小型井口吸力锚直径2.9米,高度7米,重量22吨,用海洋地质十号船在南海某31米深的浅海区域进行了原理性验证和科学探索试验,试验共进行了3个站点的沉贯安装,获取了大量的一手数据,依据数据修正了最初的理论计算公式和运算依据。通过小吸力锚原型机的试验,科研人员掌握了井口吸力锚承载理论计算方法,攻克了深海“吸盘”应用的首要难题。
钢筋铁骨其难制——钢结构加工精度控制难度大
在满足强度的前提下,内外钢筒型井口吸力锚在选材上均采用海上专用薄壁钢板,钢板厚度与直径相比非常薄。例如,为水合物试采选择的吸力锚外径为6.5米,高度12米,外筒壁厚仅为0.03米,卷制成形的外筒,横置地面就会因重力作用而成为椭圆状。受公路运输限制,外筒制作钢板的宽幅一般不超过2.5米,因此高度12米的外筒最少需要卷制5个外筒短节才能拼焊组装而成。确保单节筒体的圆度和拼装后整体外形精度是建造吸力锚需要重点考虑的问题。这是因为吸力锚在沉贯安装过程中受压差作用,外筒受海水向内挤压力,在压差作用下穿透泥层时,如果筒体建造时有变形,将有可能发生筒体受力不均而被吸瘪,造成事故。因此,对吸力锚外筒制作圆度的要求非常高。
深海井口吸力锚的设计建造,采用我国火箭建造的灵感,选择 “三垂模式”,即垂直总装、垂直测试、垂直转场,从卷制单筒开始,在地面平台上将其垂直调制到标准圆度后,一节一节向上对接组装,远程采用经纬仪时刻监测对接精度和垂直度,从而一举解决了大型“吸盘”钢结构加工精度控制的难题。
为了增加吸力锚的承载力,科研团队对吸力锚的锚顶创新性设计了“上拱下锥”型结构。锚顶上部的拱形结构,如受力拱形桥,大大提高了吸力锚的纵向承载能力;锚顶下部的锥形结构,对吸力锚起定心作用,大大增加了吸力锚的稳定性,同时提高了井口吸力锚整体横向载荷的承载能力,使“吸盘”产生更大的吸附作用。
根深柢固自难纵——沉贯安装精度控制难度大
井口吸力锚承受着来自四面八方的载荷作用力而自岿然不动,如“吸盘”般抓附在泥面上,其中奥秘与吸力锚安装时的精确控制有关。首先,吸力锚的安装垂直度要求非常高,若“井口防喷器”的超大重量作用在一倾斜锚顶上,显然会造成失稳从而失效;其次,吸力锚安装的速度,需充分考虑筒体沉贯时与泥层的作用时间,若吸力过大,沉贯过快,将造成原状土破坏,筒内部土体受吸力影响而出现膨胀,使得吸力锚安装不能到位,同时也大大降低“吸盘”的吸附能力,达不到设计要求。
为解决沉贯安装控制难题,需要制定科学的安装方案。在将吸力锚悬吊至海底泥面后,开启波浪补偿功能,消除因海上波浪影响出现的起伏不定,避免贯入过程中吸力锚反复升降造成地层液化。当吸力锚在抽吸贯入时,起重机仍需提供一定的垂直拉力;同时根据理论计算数据,严格控制安装速度和压差,时刻观察锚顶监测仪器对姿态参数的监测数据。若发生垂直度偏差,立即停止沉贯并向内泵入海水,将吸力锚向上起拔至竖直如铅垂状态,如此反复直至安装到位。沉贯安装时,操作者应严格按照方案执行,否则会功亏一篑。
用以济世——深海“吸盘”在我国的应用
2020年,我国进行天然气水合物第二轮试采,要求采用井口吸力锚技术,吸力锚竖向承载不低于500吨。井口吸力锚在我国的应用尚属首次,如此大型的深海“吸盘”研发,对我国科研人员提出了极大挑战。
由中国地质调查局相关单位组成的科研攻关团队,在小吸力锚探索取得经验的基础上,采用10余项专利技术和建造“三垂模式”,研制了新型的深海“吸盘”:直径6.5米,高12米,重量96吨。2019年11月,在南海神狐海域1 238米水深处,科研团队将中国第一个深海井口吸力锚成功安装到位。经测试,深海“吸盘”的承载力达到了技术要求,安装垂直精度控制在0.17度,远远高于0.5度的设计指标。
在吸力锚安装过程中,科研人员采用了遥控技术监控吸力锚的姿态,在甲板上可以直观地看到吸力锚的垂直状态和沉贯深度;在安装工艺方面,采用了“步进间歇式自贯”和“拖曳连续式负压贯入”工艺,最终实现了吸力锚的高垂直精度安装。此次井口吸力锚的安装成功标志着我国已经掌握了深海井口吸力锚技术,实现了井口吸力锚设计理论、建造和安装技术的重大突破,不仅满足了第二轮天然气水合物试采对井口吸力锚的要求,同时也突破了此类深海装备被国外“卡脖子”的技术壁垒,使我国从技术空白一举跃升为与国际水平并跑的拥有深海井口吸力锚技术装备的国家。
其见义远——深海“吸盘”的深远意义
深海井口吸力锚为海上油气开采提供安全稳定的井口基础,可批量应用于海域水合物产业化开发。利用深海“吸盘”可提供高承载力特点,可广泛应用于深海,为海底采油树、海底大型结构物提供基础支撑。同时,海上风力发电是世界上发展最快的绿色能源技术之一,欧美海上风电场已处于大规模开发的前夕,我国沿海水深100米以内的适用于海上风电发展的海域面积辽阔,而且距离电力负荷中心(沿海经济发达电力紧缺区)很近,具有庞大的海上风电市场。
在我国,海上风电近几年刚刚起步,因吸力锚具有施工速度快、施工成本低、基础可回收等特点,海上风电基础越来越多地采用吸力锚结构作为承载桩基础。目前风电吸力锚导管架基础是海上风电基础的首选设计,随着我国对清洁能源需求量的增长,随着“双碳”战略向纵深推进,神奇的深海“吸盘”将会有非常广阔的前景。
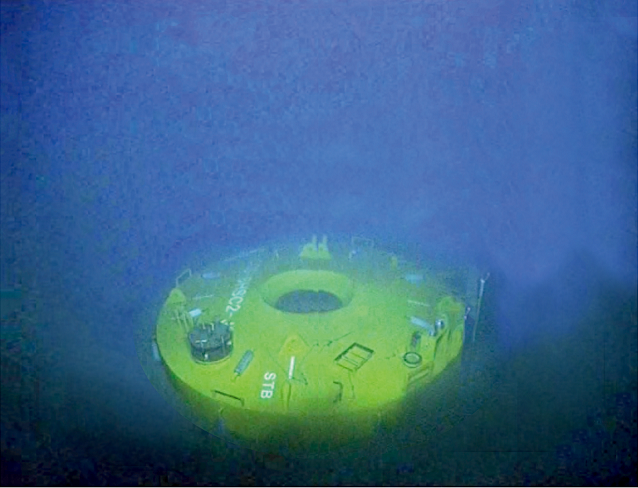